New ways of thinking
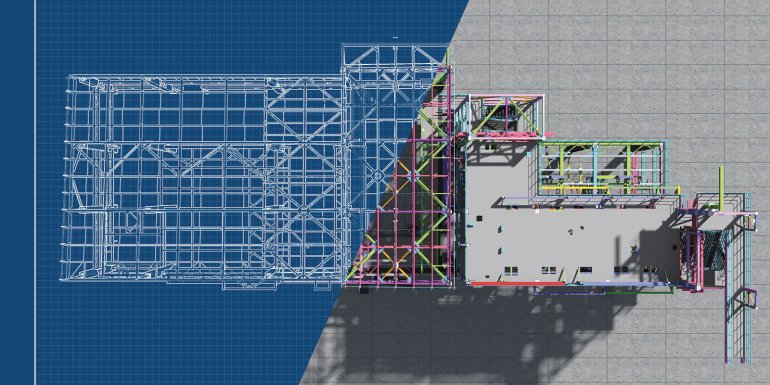
Elecosoft’s David Simpson and Mark Chapman discuss how different ways of thinking, planning and doing can streamline operations.
Construction companies are under intense pressure to run programmes efficiently. Increasing costs and complex schedules make it hard to complete projects on time and within budget. Traditional management techniques can’t always deliver the right result, so the idea of lean construction is gaining traction.
Lean construction is a project planning and management methodology. It’s an alternative to the waterfall method traditionally used in the construction industry. Rather than designing and planning up-front, lean construction uses a dynamic model. Work is broken down into short phases, and teams focus on completing a specific set of tasks. All tasks must be completed before moving on to the next phase, eliminating gaps in work. Lean construction is more collaborative and iterative than the waterfall method. Teams give input in real time, rather than being handed a schedule and only commenting when there’s a problem.
The easiest way to understand lean construction principles is to think of a restaurant kitchen. The chef will design the menu and order the ingredients ahead of time, but they’ll only start cooking dishes once service begins and they receive an order. The chef will communicate continuously with kitchen staff and front of house, tailoring dishes to each customer. They’ll also report back any changes to the menu as service continues. By collaborating, the restaurant team satisfies customers while running a profitable, waste-efficient operation.
Many benefits
Lean construction is good because it promotes stronger teamwork, open communication and continuous collaboration between project stakeholders. It helps integrate design and building, as changes are made in real-time based on conditions and customer demands, while better planning reduces time and resource wastage. Focusing teams on specific objectives streamlines the construction process.
It also helps people to work efficiently, as they can’t move on to the next phase until all tasks are complete. Teams can workshop problems and identify solutions, preventing downtime. Lean construction budgets are planned around target value delivery (TVD) – project managers establish a target cost and teams must deliver to that figure. This ensures more projects finish within budget and incentivises teams to make profitable decisions. Lean construction can reduce project costs by 10-30% compared to traditional building projects.
Moving to lean construction principles, however, involves a complete mindset change, so start small. Run a pilot to show the benefits of lean construction for projects and iron out any initial issues. Ensure the whole team understands the process as it relies on collaboration. Technology is needed here, and everyone will need access to the project management system.
Long term, the most important principle of lean construction is making iterative improvements – learning from every completed project and applying those learnings to the next. Finally, consider how you measure the benefits of a lean construction approach. Tracking and measuring improvements is made possible through performance monitoring data. KPI reporting will prove value to colleagues and achieve better results for customers.
Unleash 4D BIM
4D BIM has long been hailed as the magic bullet for project planning within digital construction, yet outdated perceptions have prevented the process from reaching its true potential. The notion of 4D BIM is not a new idea within digital construction – its potential to achieve greater precision on construction timelines and minimise financial risk is well-known by business leaders and planning teams alike. Despite high levels of awareness, the way 4D is currently being used remains fundamentally flawed. A reliance on outdated 2D processes and a lack of understanding of 3D models as effective planning tools has meant that 4D BIM has a perception problem – it’s no longer being seen to add value to construction projects.
Teams need to actively use 4D models to plan and forecast, updating as they evolve, rather than passively using the designs as a visualisation tool.
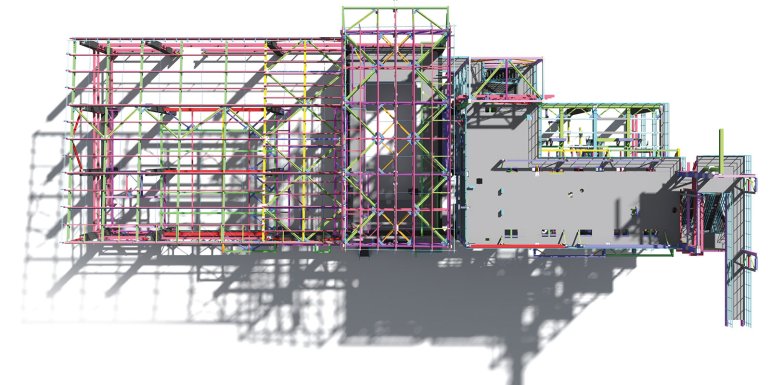
As it stands, construction teams are still opting for inaccurate planning methods. 2D Gantt chart-style formats initially form the basis of 3D models. 4D BIM is then possible by integrating project scheduling information, turning 3D models into detailed planning tools. The issue is that once projects progress, 4D BIM is quickly abandoned in favour of the tried-and-tested but ultimately flawed 2D format. Should a client request an updated 4D model further down the line, planning teams must then scramble to obtain a revised version – a costly and timely exercise, as well as an illogical one.
The process of creating 2D Gantt charts can take months, depending on the complexity of the project. Major infrastructure projects, such as airports or nuclear power stations, require the creation of hundreds of data fields, each containing project specifics. This approach also requires time-intensive manual input from across multiple teams, be it the architect, engineer or contractor. This approach then fails to record the level of detail and nuance needed at each stage of construction.
This is where what Elecosoft calls active 4D comes into its own. It splits project planning into two chains of thought – passive and active – with passive being the use of a 3D model simply to visualise plans once data has been manually entered and active making more dynamic use of data, understanding construction timelines and calculating risk.
By using the 3D model during the entirety of the planning process to ensure that the programme is correct, it allows for a deeper level of information to be attached to design plans, using data linked to digital objects for greater oversight and future-gazing. It means greater precision around risk and cost calculations, as well as a more informed client who understands the necessary timeframes for completion.
Given that the industry’s approach to project planning and scheduling hasn’t seen meaningful change in nearly a decade, it’s no surprise that widespread project overrun is now standard practice. In fact, a study by Cornerstone Projects, an underground utility provider, found that the main cause of project overrun in 2022 was poor original planning and unrealistic scheduling. What’s more, some nine in ten construction professionals experienced project delays last year – a rise of 6% since 2016. If the sector is serious about fixing its productivity problems, then methods such as active 4D should be embraced with open arms. At a time of wafer-thin profit margins, 4D BIM could be the tech they’re looking for.
For more, visit elecosoft.com