Whale watching
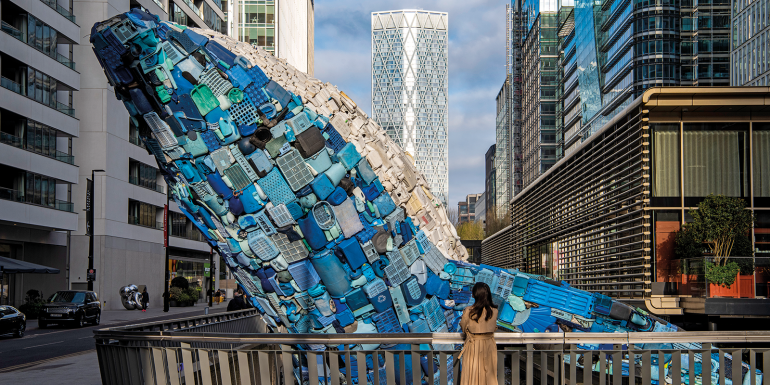
Holcim UK has created an innovative coffee concrete mix to support a 12m high sculpture in London’s Canary Wharf that makes a statement about waste.
In the biblical story, what became apparent to Jonah over three days in the belly of the whale was that it is not possible to run away from your responsibilities. In a similar way, the Whale on the Wharf by StudioKCA, created from plastic waste recovered from the Atlantic and Pacific oceans, highlights that we all need to face up to climate change.
Sited in a wet dock in Canary Wharf’s Wood Wharf district, the four-storey-high sculpture required firm counter-weight foundations. So, Canary Wharf Group turned to Holcim UK to develop an innovative concrete to support both the statue and the circular economy message it embodies.
Holcim devised a concrete mix containing biochar sourced from coppiced UK fast-growing hardwoods and, surprisingly, spent coffee grounds from Canary Wharf’s cafes and restaurants. 32 cubic metres were delivered to site.
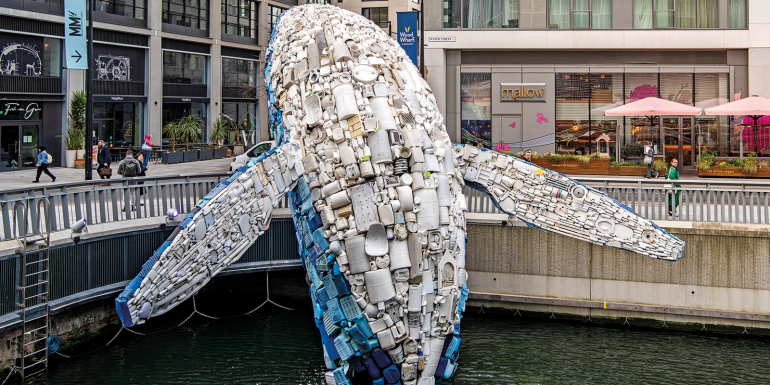
Out of the blue
Holcim has been testing the use of biochar in ready-mix concrete for a number of years. Biochar is produced by heating biomass – typically sourced from surplus wood – at temperature and in the absence of oxygen through a process called pyrolysis. The result is a black carbon-rich material like charcoal. Similarly, spent coffee grounds can be turned into a carbon-rich biochar when treated through pyrolysis.
When biochar is added to concrete, it is trapped and prevented from returning into the atmosphere as CO₂. Through using biochar, less virgin or primary aggregate is used, preserving natural resources for longer. Less waste is also sent to landfill or incinerators.
The mix produced to support the whale sculpture was formulated with limestone fines and ground granulated blast-furnace slag (GGBS). GGBS is a byproduct of the steel manufacturing process where molten slag is rapidly quenched and then ground into a fine powder. Using GGBS in concrete can reduce the embodied carbon by replacing some traditional Portland cement. The same is true of limestone powder, which is a readily available material in the UK (adding 5% limestone powder can reduce CO₂ emissions by about 5% per cubic meter of concrete, according to Construction Management Magazine). With the addition of the biochar, the embodied carbon was able to be lowered by a further 66%, yielding an impressive next-generation concrete.
Jasen Gauld, National Concrete Solutions and Product Development Director for Holcim UK, said: “It was essential that the concrete conveyed a message of circularity, sustainability and a bold approach to tackling carbon. Dubbed the ‘Bio-Expresso biochar’ in our labs, the final ready-mix concrete is fully code-compliant and performs just as expected. Plus, we have incorporated a biomass material that can lock CO₂ into the concrete, while recycling waste that would normally decompose and release greenhouse gases.”
For more information visit holcim.co.uk