CABE Building Health, Safety & Wellbeing Award
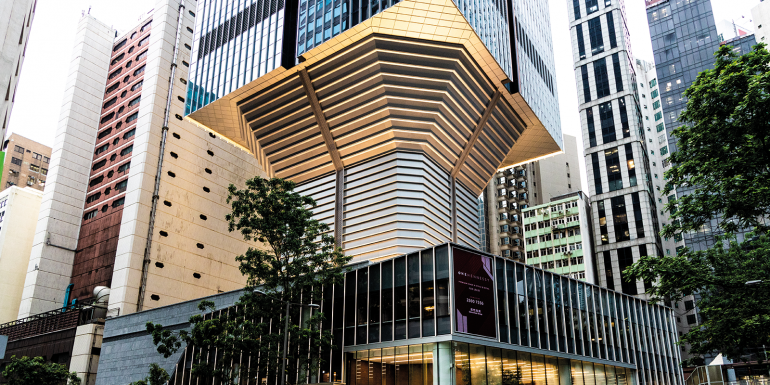
Winner CR Construction Company Limited for One Hennessy, Hong Kong, for its commitment to exemplary health, safety and wellbeing management in the construction industry.
Trying limitations and logistical challenges were met with defiant innovation during the construction of One Hennessy. The inverted pyramid structure at the core of the 32-storey new build may have posed logistical challenges, but it also presented an opportunity for exemplary health, safety and wellbeing management – especially for site workers, who were able to manoeuvre safely using a passenger hoist fixed to a temporary steel platform with a mast able to transfer lateral loads.
The inverted pyramid structure was made possible by specially designed timber formwork, 3m-deep tension beams and a belt truss. Inclined columns and timber formwork supported by thousands of inclined tie rods reduced deflection to ensure accuracy. With advanced prefabricated works off-site, and modularisation that reduced site activities, the project is a fine example of building engineering. Here is
CR Construction Company Limited’s winning entry.
Quality
CR Construction Company Limited (CRCC) commenced work on the new 32-storey commercial office tower in November 2016. Construction of this landmark development in Wan Chai, Hong Kong, was completed in February 2019. The resulting One Hennessy is unique in structural form, named No. 4 in the Top Ten Most Iconic Asian Buildings 2000 to 2020 by PRC Magazine.
To construct the single 160m-high, Grade A office building with an inverted pyramid structure at its core, the team had to operate in a congested working space with limited site access for five months. Even finding room for tools and machinery was a logistical challenge. CRCC’s role in designing and implementing effective work schedules, logistics planning and fostering team spirit through an ‘open communication policy’ among all stakeholders was the prime contributing factor to the project’s success.
Winner in numbers
The total site area is 1,951m2
Gross floor area is 29,264m2 the development consists of 21 office floors, a podium roof garden, 3 storeys of podium and one level of basement car park providing a total of 28 private car parking spaces
The height of the building is 149m with spectacular funnel-shape design between tower and podium portion
30m in height that allows natural lighting and ventilation
80% of building materials were regionally sourced
90% of construction and demolition waste was diverted from landfill
75% of the permanently installed wood products were sourced from sustainable forest (fsc certified)
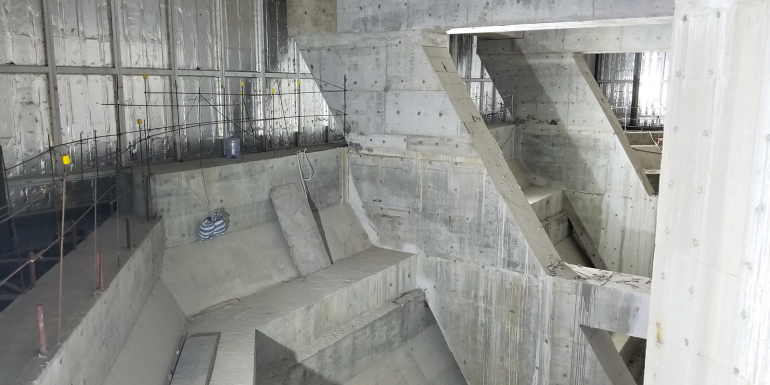
An inverted pyramid structure formed from reinforced concrete is at the building’s core
The inverted pyramid structure is located between 7/F and 10/F, with eight inclined, mega-size columns connected to the 7/F central core wall at one end and 3m-deep tension beams at the other end on 10/F. Specially designed timber formwork was used for the construction of transfer structures including the inclined columns, 3m-deep tension beams and the belt truss, which was supported by a combination of heavy-duty scaffolding (ring-lock) and traditional scaffolding. The falsework was supported by a custom-designed temporary steel deck at level +31.75mPD.
As the 3m-deep beams on 10/F are supported by inclined columns on one side, any slight deflection in the inclined columns could have caused huge distortion to the whole building. Furthermore, the inclined structure is covered by a modular metal cladding system, which makes the tolerance in the construction of the reinforced concrete (RC) structure very stringent. To reduce deflection in the inclined structure, the 3m-deep beams were pre-cambered at the end supported by inclined columns, and specially designed timber formwork supported by thousands of inclined tie rods was used to ensure accuracy when casting the inclined columns.
Impact
A temporary steel platform was used instead of traditional falsework, the latter of which occupies all the space from the 3/F podium down to the basement (foundation) floor, suspending the progress below the transfer structure and also involving a huge amount of falsework material on-site. The temporary steel platform created extra space to store machinery, tools and materials. Less material was delivered on-site, meaning CO2 emissions during the logistics process could be reduced as well. Minimising the amount of scaffold (3/F to 7/F) meant the maximum scaffold height was reduced from (18.9mPD to 52.9mPD) to (33.125mPD to 52.9mPD), so the associated risks of working at height were also reduced.
The impact on site logistics was reduced due to limited space at the site entrance and unloading area. Modular construction and off-site prefabrication for the riser pipe was adopted, with the pipe module being delivered by the vertical transportation facility and assembled on-site. The modularisation benefited the project by using advanced prefabrication works off-site, reducing subsequent site activities and time on-site, and improving site environment control.
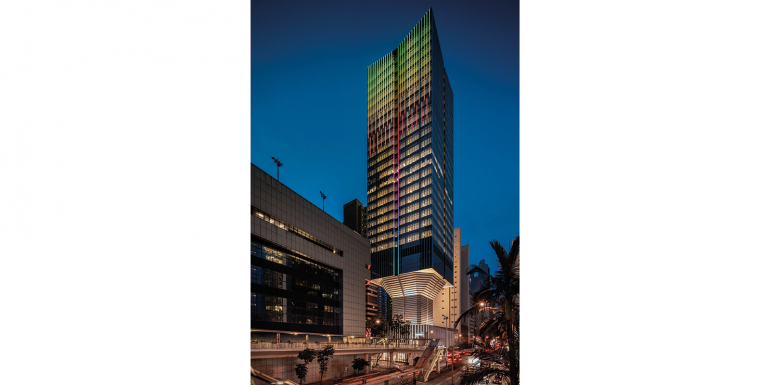
Sustainability
Sustainability has been a key pillar of the One Hennessy construction project. The project team is committed to environmentally-friendly construction and gave in-depth consideration to how the practices would impact the community.
The project supported green construction, implemented energy-saving measures throughout the building, engaged with stakeholders and the government on sustainable initiatives, and organised community activities to foster environmental awareness. A Sustainability Task Force was set up to formulate the roadmap for the project and reduce carbon emissions.
Low-absorptive materials were used in the building’s envelope to maximise natural light penetration and minimise energy and heat loss. Rooftop vegetation serves to mitigate the urban heat island effect. One Hennessy achieved the internationally-recognised LEED Platinum Rating for Green Buildings and the construction project is recognised by the Hong Kong Green Organisation. During the construction of One Hennessy, more than 90% of construction and demolition waste was diverted from landfill. Approximately 10% of recyclable materials (including steel and paper) were recycled through authorised recyclers. The building operator used waste separation bins to separate and collect wastepaper, plastics and metals. Additionally, the project participated in the Toner & Ink Cartridges Recycling & Reuse Programme by Friends of the Earth (HK) and the Rechargeable Battery Recycling Programme by EPD of the Hong Kong government.
For One Hennessy, more than 80% of the building materials were regionally sourced. More than 75% of the permanently installed wood products were sourced from sustainable forest (FSC certified). Energy simulation was adopted to estimate energy use. Modularisation and prefabrication technology was adopted, too; for example, a prefabricated pipe riser module and plant main header module were used in the water chiller plant.
Inclusivity
As the project’s main staircases are located in the centre of the building without windows, it would have been a major challenge to walk all the way along the cramped staircase to more than 21 floors during construction period – especially in summer. In consideration of the health and safety of site workers, a passenger hoist was installed on the podium flat roof to provide quick access from 3/F to the upper floors.
To provide lateral stability to the system, wall ties needed to be installed with designed spacing linking the passenger hoist and the building. Due to the building’s inverted pyramid form, the RC structure was too far away from the passenger hoist between level +45.20mPD and +18.90mPD, making it impractical to have conventional wall ties. As an alternative, a single mast was installed next to the passenger hoist to help provide lateral support. Fixed to the temporary steel platform, the mast was able to transfer lateral loads from the passenger hoist to the steel platform, and then to the core wall of the main building. This innovative solution has been proven to be the most efficient way to provide stability by integrating with existing temporary structure. The structural integrity of the temporary steel platform under the additional load from passenger hoist was checked thoroughly. The passenger hoist also provided a benefit to older employees – a small cost bringing big non-financial benefits in caring for workers, which ultimately has a positive impact on productivity.
Client/user satisfaction
To overcome challenges such as site logistics and those posed by the inverted pyramid structure, the construction team planned the necessary work sequences and activities with flexible contingency and scenario plans. This eliminated delays and/or time implications and had minimum cost implications, which pleased the client.
Quality control was evident at every stage. For example, the inverted pyramid, RC structure is not only essential to the structural integrity of the whole building, but it is also the most eye-catching part of the façade. To provide a nice surface for the cladding installation, very stringent tolerance is allowed and so an independent surveyor was employed.
Quality control included fulfilling environmental obligations, too. For the headroom requirements of office design, a gypsum block wall system with high sustainability was chosen. A lightweight material with considerable load-bearing capacity, gypsum block is space saving and enables fast installation and easy alteration. It also works excellently in terms of modifying the building’s internal environment including moisture control, sound insulation, waterproofing, fire resistance and thermal insulation. Moreover, it helped enhance site safety, reducing material wastage and saving energy. International environmental standards were incorporated, eg 14001, 14064 and 50001. Energy-saving measures were also implemented throughout the course of construction in collaboration with the client to uphold sustainability values in developing environmentally-friendly properties.
The passenger-hoisting facility was the first of its kind in Hong Kong, utilising a unique construction method to enable the vertical transportation of this 150m-high building, reflecting the team’s determination to overcome site constraints and provide a good working environment for employees and workers.
CABE’s conclusion
The key to this project’s success was having a well co-ordinated team of people with the right skill sets following thorough and well-considered workplans (which detailed the project objectives, requirements, organisation, roles, responsibilities and communication procedures).
CABE member and project manager for One Hennessy,CY Wong, was responsible
for the overall construction process, monitoring andco-ordinating with an effective open-communication policy that encouraged knowledge sharing and flexibility. This led to ease of implementation, cost-efficiency and a good work culture on-site.
The environmental measures such as rooftop vegetation to mitigate the urban heat island effect and the building’s envelope, which maximises natural light and minimises energy loss, helped One Hennessy achieve LEEDs Platinum Rating for Green Buildings. In the construction of One Hennessy, more than 80% of building materials were regionally sourced, and 90% of construction and demolition waste was diverted from landfill.
A standout of the project is, perhaps, the technical skills shown in overcoming the difficult logistics of the site and that, given these, great care and attention was paid to the workers’ safety and comfort throughout.
As CY Wong notes: “A happy workplace was provided by a good working culture. Our wellbeing is taken care of at work, where the team maintain a naturally low turnover and high productivity.”