Toughened glass failures led to near-miss
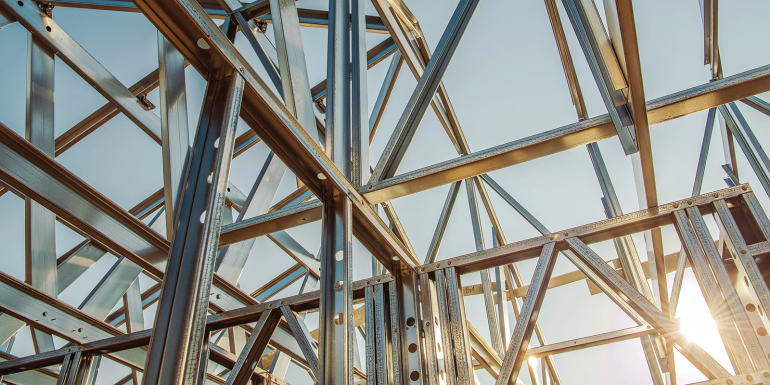
Glass produced by some processors has not been properly heat-soaked and is, therefore, much more likely to shatter in use
A reporter believes from their experience that toughened glass that has been heat-soaked in compliance with BS EN 14179 is many times less likely to shatter spontaneously than toughened glass that has not been heat-soaked. Consequently, many designers specify heat-soaked toughened glass to minimise the risk of broken toughened glass falling from buildings. Nevertheless, glass has fallen from buildings – there have been near misses and people have been alarmed by breakages.
According to the reporter, failures caused by nickel sulphide inclusions (the impurities that heat-soaking counteracts) are very rare in heat-soaked toughened glass provided by most processors. However, there do appear to be cases of failure to heat-soak the toughened glass properly, if at all, by a few processors.
The reporter and colleagues have analysed the number of breakages caused by nickel sulphide on several buildings where the glass was sold and CE marked as being heat-soaked and compliant with BS EN 14179. They found that the number of breakages was much higher than expected. This was evidenced by the statistical improbability of properly heat-soaked glass failing at the rates observed on affected buildings. Where a high rate of failure was observed, factory records of the heat-soaking process tended to be absent, untraceable to the actual glass delivered or visibly altered in a way that is not consistent with human error. The analysis led to the finding that the rates of failure on affected buildings were not credibly consistent with the claim that the glass was heat-soak tested.
The reporter goes on to say that it is not possible to examine, test or check toughened glass when it is delivered to ensure that it has been heat-soaked as marked, so reliance is placed on documentation and marking by the producer. Those responsible for buildings had no indication that anything was amiss with the affected toughened glass, which they understood to be heat-soaked, until a number of panes shattered, the origins of failure identified, retrieved and analysed, and the rate of failure compared with the expected probability distribution. It could take several years for the pattern of failures to emerge and be recognised, during which time people were exposed to risks much higher than intended.
The reporter has advised those responsible for the management of affected buildings to reassess the safety of the glazing and in some cases take additional measures to mitigate the increased risk because they should assume that the glass is not heat-soaked and that further breakages are foreseeable. Protective measures such as canopies, diversion of pedestrian routes, daily inspection for broken panes, application of temporary films and re-glazing have been implemented. Property values and confidence have been damaged.
Designers rely on the declared reliability of heat-soaked toughened glass (less than one critical inclusion in 400 tonnes) when designing façades and other glass applications such as barriers, says the reporter. If the material supplied is much less reliable than that specified, the risk to people in and around those buildings is significantly increased. Broken toughened glass falling from height has the potential to cause significant injury or death, and failure to deliver glass of the agreed reliability exposes people to this unseen hazard.
The reporter confirms a trend over recent years for some designers to avoid the use of toughened glass because of the poor overall record of failures, even when heat-soaking was specified. This has resulted in the use of thicker glass to achieve strength and more use of laminated glass to achieve impact safety in situations where reliable heat-soaked toughened glass would have been adequate. The reporter argues these specification decisions often result in a higher embodied carbon impact.
The reporter emphasises that these concerns apply only to glass supplied by a very few processors, and that it is the reporter’s experience that failures caused by nickel sulphide inclusions in heat-soaked toughened glass are very rare from the majority of processors.
The reporter concludes that heat-soaked toughened glass can be reliable and efficient if properly processed. However, the only way to verify that toughened glass has been properly heat-soaked is by true and accurate records of the process having been applied to the panes of glass in question. This requires traceability and responsible practice by the processor.
Finally, continues the reporter, those specifying and procuring heat-soaked toughened glass should exercise particular care in reviewing production control measures and documentation, and may choose to observe the process directly.
Comments
The reporter raises very valid concerns. As there is no way to tell the difference between heat-soaked and non-heat-soaked toughened glass, it is hard to enforce compliance with standards at a practical level. One incident saw a number of panels fall from a tall building, all with nickel sulphide inclusions. Subsequent investigations showed that records had been properly kept and the process was followed all the way back to the heat-soaking machine, which was properly calibrated and checked. The only conclusions that could be drawn were that the records appeared anomalous and that the glass had never been heat-soaked. Incidents like this may have led some practitioners to take the approach of not allowing toughened glass when overhead or where it could fall and cause a danger to passers-by (unless the glass is part of a laminate).
Manual to the Building Regulations (page 54, F31) states: “If a material is at risk of spontaneous failure, such as toughened glass, and the consequences of failure are likely to present a safety risk, it is unlikely that the material will meet the requirements of the Building Regulations.” Monolithic toughened glass can fail without warning for a number of reasons, including impact from a sharp object, any impact when previously damaged, poor detailing, differential solar exposure or nickel sulphide inclusions. As nickel sulphide inclusions are just one cause of failure relating to monolithic toughened glass, it is arguable that designers should not rely on heat-soaking to make monolithic toughened glass safe in conditions where its failure would present a life-safety risk.
Further reading
- CROSS Safety Alert Structural safety of glass in balustrades: bit.ly/CROSSUK_balustrades
- CIRIA publication Guidance on glazing at height (C632F) at bit.ly/ciria_glazing includes information on glass manufacture and processing, as well as risk and hazards, as does the Institution of Structural Engineers’ publication Structural use of glass in buildings (Second edition) at bit.ly/istructe_structural
- Technical Note No 68: Overhead Glazing from the Centre for Window and Cladding Technology at bit.ly/CWCT_technical deals with the selection of glass to limit the risk of injury from falling glass. It is concerned with the risk of failure, failure mode and post-failure behaviour of the glazing.
Furthermore, the UK government has banned the use of laminated glass in some parts of tall residential buildings (above 18m under regulation 7 and above 11m in the approved documents). This means that the use of laminated glass in balustrades may not comply with Building Regulations. Monolithic glass used in such circumstances must comply with Part K4 of Schedule 1 to the Building Regulations 2010, which states: “Glazing, with which people are likely to come into contact whilst moving in or about the building shall - (a) if broken on impact, break in a way which is unlikely to cause injury.” Thus, any glass which if broken fails to provide reasonable containment or causes injury to those below as it falls is unlikely to comply with Part K4. It should not be forgotten, of course, that glass in buildings will likely need to satisfy a number of performance criteria including, for example, thermal and acoustic requirements.
Where heat-soaked glass is used, it is important that heat-soaking records are validated. The processes required to provide a suitable level of assurance could be extensive. The heat-soaking process weeds out the critical nickel sulphide defects by forcing the failure in the quality control process, and so the panel containing the particle does not leave as a finished product.
Caution is required where the use of temporary films is proposed when considering the risk of tempered glass failure. If the film is not properly secured, the result can be a failed tempered panel falling in a single mass rather than a distributed cloud of particles.
Designers should properly risk assess their use of glass and, because the risk of failures still remains even after heat-soaking, take account of the risk of using toughened glass where its failure would cause a hazard.
To subscribe to the CROSS UK newsletter (structural and fire safety concerns), visit cross-safety.org/uk/user/register