Cross UK Report 1275: Durability issues with engineered timber
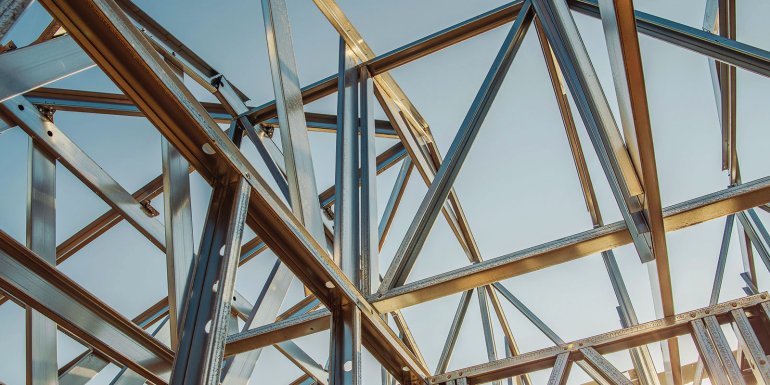
Collaborative reporting for safer structures. Report 1275: Durability issues with engineered timber.
A reporter has observed durability issues when there is water ingress or condensation issues.
While this does not necessarily relate to an issue with the engineered timber product itself, there is significantly more disintegration than with conventional timber components, which results in failure rather than distortion. Structural failure of primary support members has been observed by the reporter.
Two surveys were within developments less than 15 years old where there was significant deterioration of the engineered timber rafters and Oriented Strand Board (OSB) sheathing. The third survey was on a dwelling less than 13 years old. It was likely due to a combination of water ingress and possible condensation issues because it has been designed as Passivhaus with high levels of insulation and cold bridging. Engineered timber products were specified on the original plans, with glulam ring beams that the reporter notes have deteriorated significantly.The reporter concludes that care is needed when specifying the circumstances in which engineered timber products will be used.
Comments
It is likely the issues highlighted by the reporter are related more to poor detailing or poor maintenance with regard to water ingress and condensation than the choice of material. The problem is not so much that engineered wood products are less durable compared to solid timber, but that it is apparent that some parts of the industry need to better understand the dos and don’ts of timber-frame construction and the higher requirement for excluding water.
CROSS is aware of considerable anecdotal feedback that durability is not given the design attention it deserves – in particular the avoidance of water ingress through roof coverings, the avoidance of condensation and the limited ability to identify issues related to these before they become so advanced as to require significant remedial measures.
Report 852 Rotting of cross-laminated timber (CLT) roof panels covered similar issues: “What the reporter describes could be condensed water vapour dripping back into the building due to poor detailing or construction of the roof covering. BS 5250:2011 Code of practice for control of condensation in buildings gives guidance on the risks associated with excessive humidity in buildings, notably mould growth and condensation. Both can compromise the integrity of the building fabric. It describes the principal sources of water vapour [and] its transportation and deposition, and provides guidance on how to manage those risks during design, construction and operation.”
Typically, the onset of decay starts when the moisture content of timber is over 20%. When there is a significant amount of trapped moisture or water collected during construction, the timber will begin to deteriorate. If moisture or water is continuously fed to the timber via roof leaks and/or condensation and it is not able to dry, then the rate of decay is accelerated.
If a material is only suitable for a dry environment, then it is essential that water ingress is prevented by sound detailing and correctly applied coverings. Maintenance is similarly essential and owners should be vigilant in taking action if there are observable leaks or excessive condensation.
The use of the wrong sheathing board could also account for the sorts of defect noted within this report. The National House Building Council (NHBC) and other warranty providers have specified what sheathing material specifications are acceptable on a residential site – for example, NHBC Standards Clause 6.2.7.